МОТОГОНКИ.РУ, 9 июня 2014 - У нас Schuberth знают, в основном, по мотошлемам, которые считаются продуктом класса high-end из-за уникальных технологий и материалов, которыми владеет завод. Но вы, вероятно, также знаете, что с 2000 года немецкая компания является разработчиком и производителем, а с 2003 и официальным поставщиком шлемов для Формулы-1, в частности, Scuderia Ferrari F1. Вот оттуда родом и SR1.
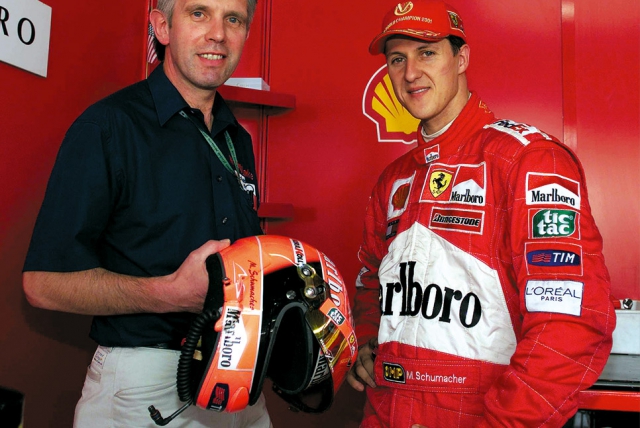
Михаэль Шумахер (Ferrari F1) в программе разработки Schuberth SF1
Магдебург тесно сотрудничает со многими топовыми авто- и мотогонщиками. Но особенно тесной и плодотворной была работа с 7-кратным чемпионом Формулы-1 Михаэлем Шумахером. Шумми сделал Ferrari чемпионом в 2000 году, с этого же года началась девелопперская программа Schuberth в F1. Немцы сделали специально для чемпионата прототипов собственный шлем-прототип, Schuberth SF1, который производился индивидуально для Михаэля. Но с 2003 года завод стал делать шлемы для всего обслуживающего персонала команды (pit-lane crew) и ее пилотов, которые после этого входили в состав - Ника Хайдфельда, Нико Росберга, Кими Райкконена, Фернандо Алонсо и Филипе Массы.
SCHUBERTH - Михаэлю Шумахеру: от SF1 к SR1
Сотрудничество с Михаэлем на этом не остановилось. Когда великий немец ушел из Формулы-1, чтобы заняться своими делами, он всерьез увлекся мотоциклами. Михаэль обратился в Schuberth с просьбой создать для него такой же удобный и легкий шлем, как у него уже был, только для мотогонок. В Магдебурге сделали SR1.
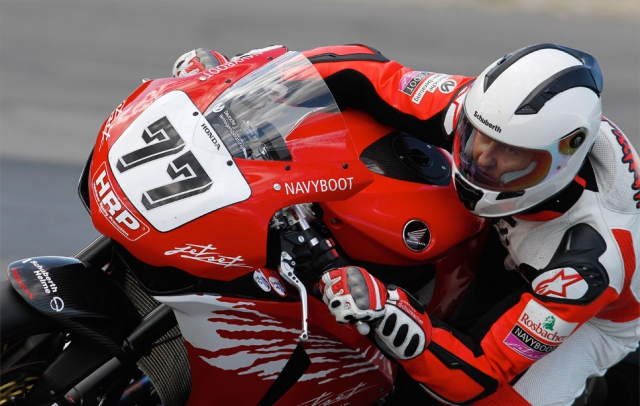
Михаэль Шумахер в серийном шлеме Schuberth SR1 2010 года
В основе прототипа SR1, появившегося в 2008, лежала "скорлупка" все того же SF1, только улучшенная: мотошлем должен был отвечать большим требованиям безопасности и стать гораздо легче. Если SF1 Шумахера весил более 1200 г, учитывая отделку и навеску, в том числе, коммуникационную систему (а "серийный" Schuberth SF1 весит 1400 г), то первый SR1 весил всего 900 г и был сделан из чистого карбона, по меркам 7-кратного чемпиона, фаната быстрых мотоциклов, участника IDM Superbike и FIM World Endurance. И вообще то, в Schuberth не планировали запускать SR1 в серию.
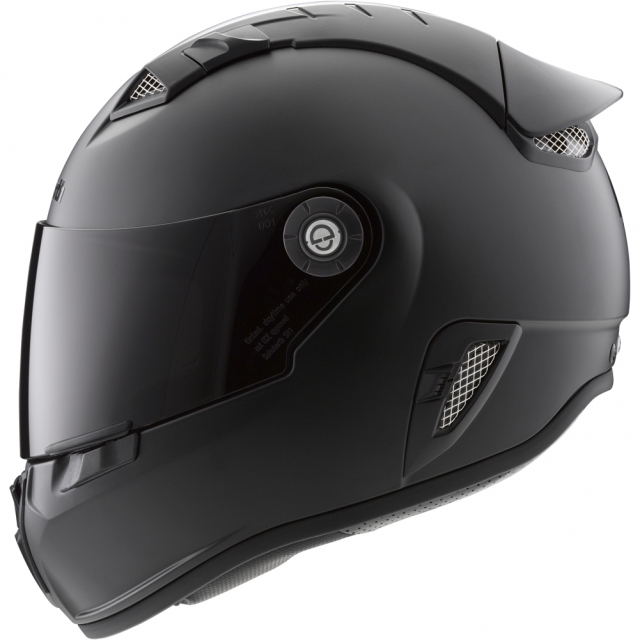
SCHUBERTH SR1 Matt Black
Тем не менее, на Кёльнском Мотосалоне 6 октября 2010 года компания представила "гражданскую" версию SCHUBERTH SR1, существенно изменившуюся и ставшую куда комфортней первого прототипа.
Эволюция Schuberth SR1: как менялась модель с 2008 (прототип) к 2014 (новая серийная модель)
Schuberth SR1, созданный персонально для Шумахера, и сегодня остается одним из секретов завода. На заказ по меркам гонщиков в год производится всего несколько десятков карбоновых реплик, цена каждой индивидуальна и не разглашается, аналогично и с SF1 для Формулы-1 и других автомобильных чемпионатов, в частности, DTM и WTCC. Фотографировать в деталях прототипы из R&D департамента не разрешили даже не телефон.
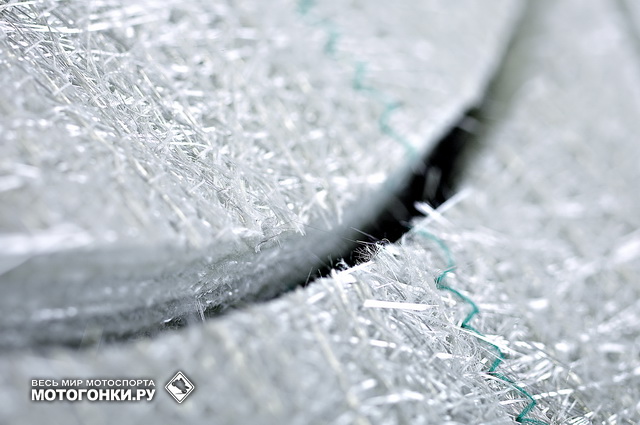
Выкройки из арамидной ткани готовы для запекания!
Гражданский SR1 отличается по материалам и, в связи с этим, по весу: многослойная прессованная ткань, из которой "выпекают" скорлупку мотошлема состоит из 6 слоев пересекающихся композитных нитей и одного слоя карбонового волокна (ткань S.T.R.O.N.G.), масса конечного продукта колеблется от 1280 до 1330 г. Модель 2014 года снабжена специальным аэродинамическим спойлером с изменяемой геометрией, 4-канальной системой сквозной вентиляции и люксовой отделкой из антибактериальной ткани Coolmax.
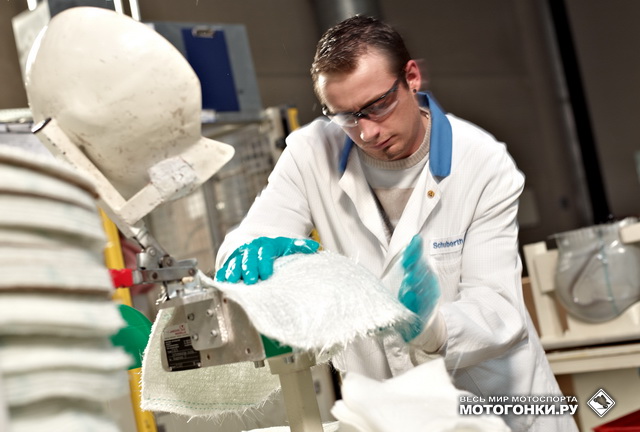
Специалист укладывает заготовки на пресс-форму
Технология производства скорлупки шлема одинакова для всех продуктов Schubert. Ткани из арамидного, кевларового или карбонового волокон прессуются под большим давлением в несколько слоев, после чего вырубаются "выкройки", которые затем пропитываются специальным компаундом (клеем на базе эпоксидных смол и пластификатором, рецепт которого является главным технологическим секретом Schuberth) и помещаются в специальную камеру, где под давлением в 4.7 bar и при температуре в 80 градусов две половинки шлема, идущие внахлест одна на другую, "запекаются" в течение 4.5 минут. Если посмотреть готовую скорлупку любого шлема Schuberth на просвет после производства, видно, что посередине она толще, но никакого шва (как у некоторых дешевых шлемов) нет и в помине - половинки становятся едиными целым. Этот процесс производится вручную, причем, после каждой операции заготовка взвешивается на электронных весах - на все есть таблица допусков. Кроме проверки заготовок на местах, они проходят еще и независимый Quality Check (QC) на каждой стадии производства.
Фото: автора и из архива Schuberth