Mass Production
Увидев, как багаж появляется на свет в виде идеи и прототипа, отправился туда, где куется серийный продукт. Роботы, плазменная резка, дуговая сварка, станки с ЦПУ: в некоторых цехах людей совсем нет, механика отлажена автоматически, в других, например, на конечной сборке важны особенности ручного труда.
Многолюдно в зале, где производятся заготовки. Немногословные рукоделы ваяют из здоровенных кусков алюминия пресс-формы будущих пластиковых изделий, в основном, кофров. Натуральное искусство, скульптура по металлу, только эти формы – секретный продукт, который никогда не выйдет за стены предприятия. Процесс можно увидеть на этом видео:
Тестовая лаборатория. На самом деле, ничего интересного, но вопросы есть. Например, почему на всех пластиковых кофрах с креплением типа Monorack максимальная загрузка только 10 кг? Как испытываются? Откуда цифры? Алессандро отвечает: это рекомендуемый гарантированный на 100500% порог, конечно, не предел физической выносливости. Рядом - Джузеппе: «А с какой скоростью обычно ездите вы?» Показываю навигатор со статистикой за вчерашний день, там 557 км пути пройдены за 4 часа – средняя 143 км/ч. Все ясно, Джузеппе улыбается: «Ну, да, обычно так наш багаж и эксплуатируется – с ветерком!»
«С точки зрения езды по шоссе, единственной нагрузкой на кейсы и крепления является набегающий поток воздуха, но жестким кофрам, разработанным для шоссейных мотоциклов и обладающим достаточной обтекаемостью и низким сопротивлением, это – семечки, - добавляет Алессандро, - А крепления Monorack и Easylock усилены арамидными волокнами, так что на статическую нагрузку (на разрыв) очень стабильны, можно не беспокоиться».
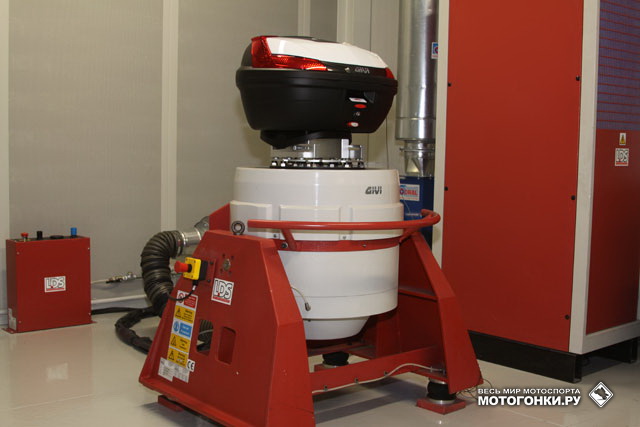
Test Lab: очередной прототип кофра на вибростенде GIVI
Что касается ударных нагрузок, то все модели проходят 5-ступенчатый тест на вибростенде. Испытания начинаются с пустыми кейсами, затем их нагружают под завязку, до 30 кг. Кейсы морозят в холодильнике, греют в печи и снова отправляют на стенд. Цикл повторяется многократно.
Единственное, что пока не удается решить в виду самой модели крепления и расположения жестких и – особенно – мягких кофров, так это снизить их аэродинамическое сопротивление и влияние на расход топлива, но это неизбежное «зло».
GIVI Town: сборочный цех и контроль качества перед отправкой на склад
GIVI Town
Логистика – еще один важный элемент компании GIVI, ведь подразделения и импортеры находятся по обе стороны океана, более чем в 40 странах мира, включая Россию, конечно же. Подобную организацию на складах я уже видел. В 2010 году. В Швейцарии. В IXS. Ребята из GIVI улыбаются и переглядываются: да, это наши большие друзья.
Гигантский ангар площадью в 10000 кв.м. и высотой 13 метров забит продукцией, при этом, только что собранные кофры, шлемы, сумки, крепеж и все такое прочее постоянно течет на стеллажи, а с другой стороны вытекает обратно – в погрузочный цех, где 5-6 компактных погрузчиков ловко закидывают упакованные заказы в фуры. Процесс непрерывный.
Головной офис (в Флеро) – он же мозговой и информационный центр компании, там расположены все сервера, а на складах (их не один, если и другие, поменьше) – клиентская часть специального программного обеспечения. Все на штрих-кодах, все автоматизировано. Для полной идиллии космопарка не хватает только белых бесшумно снующих туда-сюда роботов-андроидов. Когда отдел продаж в Флеро формирует заказ, он незамедлительно поступает на склад и идет в сборку. На сборку паллеты уходит не более 10 минут. Проверку заказ проходит дважды: в ходе сборки (штрих-сканнер просто не примет неверный артикул и продукт), а затем, в процессе упаковки – там ответная часть, которая сверяет список собранных товаров с заказом. Как только заказ пересекает «красную линию», он автоматически списывается со склада. Продано!
Посмотреть видео с тура по фабрике GIVI целиком, одним фильмом:
Фото: motofoto.ru